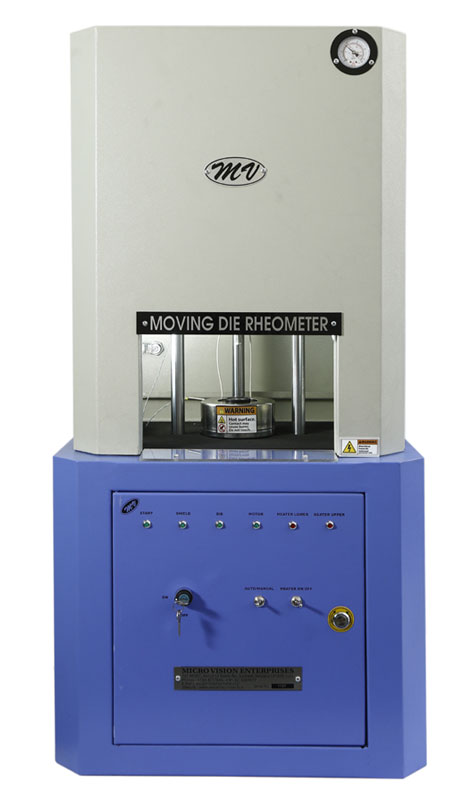
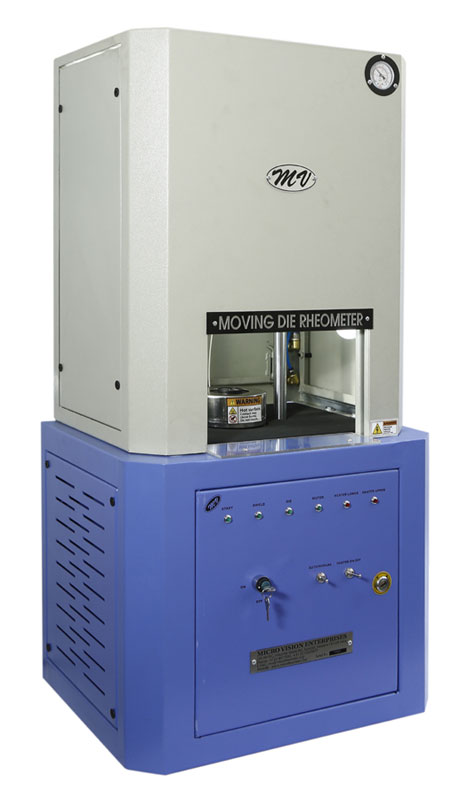
Micro Vision’s high precision instrument – Moving Die Rheometer offers sensitivity and reliability of measurement for the evaluation of Vulcanization properties of rubber.
Using world class technology, it has been developed to determine the elasticity of vulcanization, the cure rate, cure speed and examine the behavior of rubber mixture post. vulcanization, All the more, with MV’s Moving Die Rheometer , the viscous and elastic fraction of the rubber mixture.
With the help of our product, an expert can easily monitor the initial trough ie. processing behavior of the compound and the final shape of the curve.
Principle
How does it works ?
The rubber test piece is contained in a unique designed bi-conical die capacity and also maintained at a stable die temperature, Through the oscillating lower die ot small rotary amplitude. a precise transducer will measure the reaction torque of vulcanizing rubber, MV’s accurate temperature control and torque measurement ensures the later temperature response, greater repeatability and reproducibility of test result
Resulting in measurement of accurate scorch time and cure time, it can accurately measure and analyze the viscous and elastic properties of vulcanizing rubber.
Definition of S' and S"
s’ is called the storage modules, elastic modules or in-phase modules. S” is called the loss modules, viscous modules, or out-of-phase …
‘The minimum torque is proportioned to the viscosity of the uncured compound. ‘The scorch time is a measure of process safety. ‘The full curved torque is a measure of shear modulus or stiffness of the compound.
As per “Rubber World* 1990 January article “New Rheometer and Money Technology” by Patrik |DiMauro, Monsanto Company, and I. Derudder and I.P.Etienne, Monsanto-Furope, one can appreciate that the results variation between original model and later models is quite substantial especially the times values. This is purely because of better temperature control and recovery Tests conducted on a BR compound at 177 C in 50 new machines of each type i.e. ODR and MDR, the difference can be summarized as follows:
- Torque Values: ML is lower in ODR 2000 then R100S, MH is slightly higher in ODR 2000 then RIOOS. ML & MI-1 are much lower in MDR due to different design of machine and the dies.
- Time Values: -Time values are faster in MDR then ODR
- Sensitivity: The sensitivity of the machines with respect to variation in ingredient was also assessed and it was found that the difference between B-1005, ODR and MDR was insignificant. Any difference Foot iced was purely due to better temperature control and recovery.
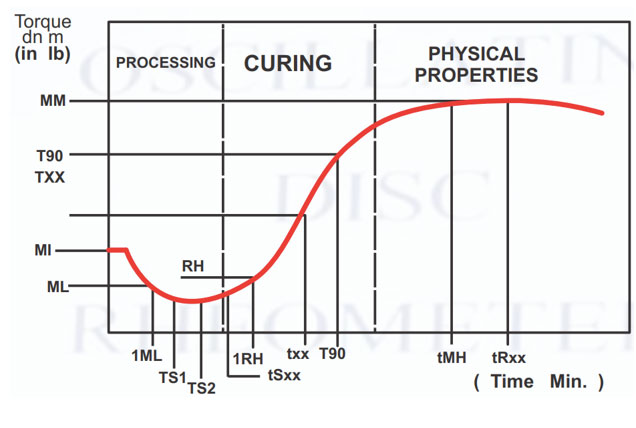
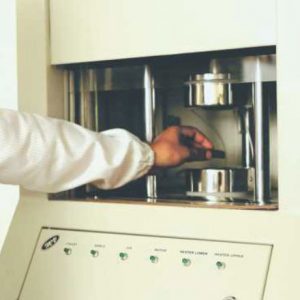
Reduced Operation Time
In MDR Directly heated dies reduce testing time and allow 25-50% more tests than conventional ODR
Easy sample removal from the die.
Self-calibrating temperature setting
Operation
“MV” Moving Die Rheometer (MDR) measures the cure characteristics of compounded rubber by using a sealed rotor less moving die system. At the start of a test sample is loaded between the heated dies which are closed pneumatically after the protective shield has been automatically lowered. The lower die is then oscillated through a preset angle (0.5 C). The lower die oscillates at 1 66 H7. The reaction torque measurement system of the MDR eliminates mechanical friction to provide precise values for elastic modulus S’ (torque) and viscous modulus S The reaction torque transducer measures the torque through the sample from the lower die.
‘The signal of force (torque) is sensed by the sensor, converted volts and then through ADC fed into the computer to draw torque against time cure, the Moving Die Rheoreter sealed, rotor less, moving die system has improved capability to detect compound differences. It minimizes the sample slippage at high strains as compared with unsealed system.
SPECIFICATION
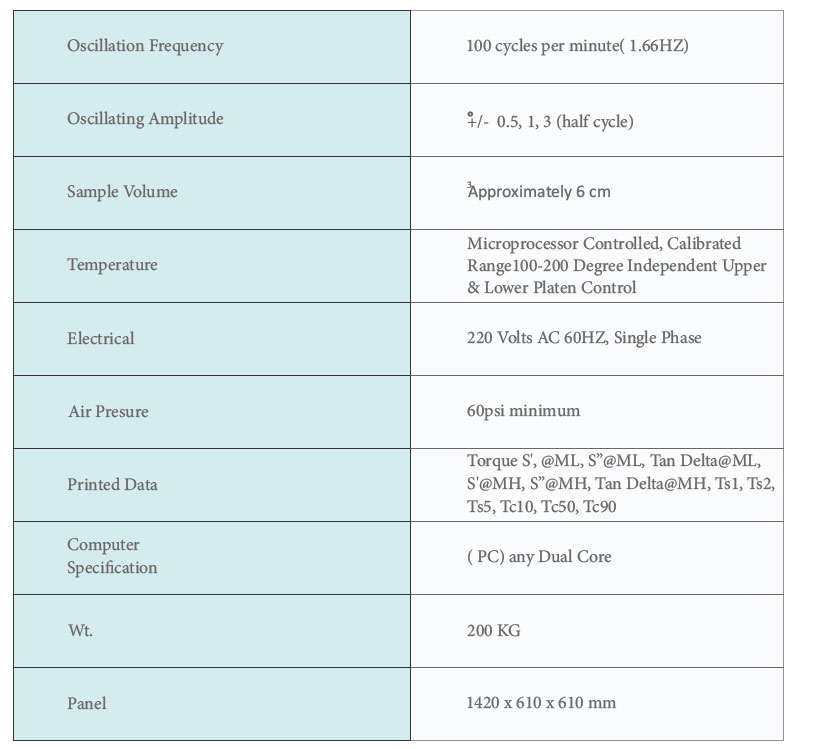